In the world of inventory management, keeping track of stock levels is crucial for businesses to ensure smooth operations and avoid stockouts or overstocking. One tool that aids in this process is the bin card, which helps track the inventory levels of a specific item in a specific location.
While a store’s ledger is used to track the overall inventory levels of all items in a store or warehouse, the bin card provides a more detailed and specific view of individual items.
This article will explore what a bin card is, how it works, the difference between a bin card and a store’s ledger, and provide a step-by-step guide for implementing a bin card system.
What Is A Bin Card?
A bin card, also known as a stock card or bin tag, is a document used to track the inventory levels of a specific item in a specific location. It provides a detailed record of stock movements, including receipts, issues, and balances. The bin card is usually kept in a physical bin or storage location, hence the name, to ensure easy access and visibility of the item’s stock status.
Bin cards are commonly used in industries such as manufacturing, warehousing, and retail, where efficient inventory management is essential. They serve as a tool for inventory control and help businesses keep track of stock levels, reorder points, and identify any discrepancies or irregularities in stock movements.
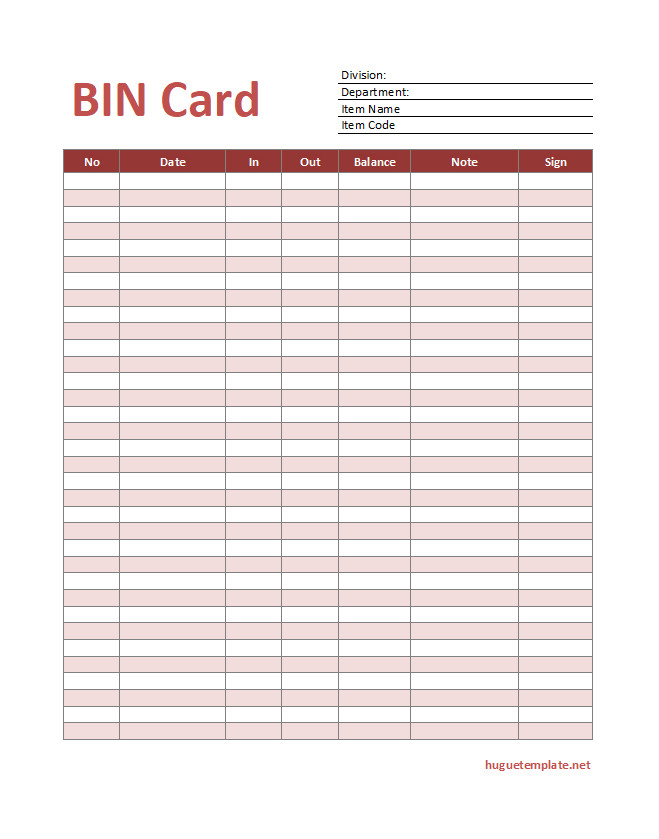
How Does Bin Card Work?
The bin card works by recording all the relevant information about a specific item’s stock movements in a particular location. It follows a simple and systematic process to ensure accurate tracking and control of inventory. Here’s how it works:
- Receipt of Goods: When new stock arrives, the bin card is updated to reflect the quantity received, along with details such as the date, supplier, and any other relevant information.
- Issues of Goods: Whenever a stock is issued or taken out from the bin location, the bin card is updated to record the quantity issued, along with details such as the date, recipient, and purpose of the issue.
- Balance Calculation: After each receipt or issue, the bin card is updated to calculate the new balance of the item in the specific location. The balance is determined by subtracting the total quantity issued from the total quantity received.
- Reordering: By regularly monitoring the bin card, businesses can identify when stock levels approach the reorder point. This enables timely reordering and helps prevent stockouts.
- Stocktaking: Periodic stocktaking is conducted to reconcile the physical stock with the balances recorded on the bin card. Any discrepancies are investigated and corrected to ensure accurate inventory records.
The bin card provides a comprehensive and detailed history of a specific item’s stock movements, making it an invaluable tool for inventory management.
Difference between Bin Card and Stores Ledger
While both the bin card and the store’s ledger are tools for inventory management, they serve different purposes and provide different levels of detail. Here are the key differences between the two:
- Scope: The bin card focuses on tracking the inventory levels of a specific item in a specific location, providing detailed information about that particular item. On the other hand, the store’s ledger tracks the overall inventory levels of all items in a store or warehouse, providing a broader view of stock levels.
- Level of Detail: The bin card offers a more granular level of detail by recording each transaction related to a specific item. It captures information such as receipts, issues, balances, and other relevant details. In contrast, the store’s ledger provides a summary of stock movements, typically in terms of total quantities received and issued, without the same level of transactional detail.
- Location: The bin card is kept in the physical bin or storage location of the specific item it tracks. This ensures easy access and visibility of the item’s stock status. In contrast, the store’s ledger is usually maintained electronically or in a centralized location, providing a consolidated view of stock levels across multiple locations.
Benefits of Using Bin Cards:
- Accurate Stock Tracking: Bin cards provide a detailed record of stock movements, helping businesses accurately track inventory levels.
- Prevent Stockouts and Overstocking: By monitoring bin cards, businesses can identify when stock levels approach reorder points, enabling timely reordering and preventing stockouts or overstocking.
- Improved Inventory Control: Bin cards allow for better control over individual items and locations, ensuring efficient inventory management.
- Identify Discrepancies: Bin cards help identify any discrepancies or irregularities in stock movements, enabling businesses to investigate and correct errors.
- Enhanced Decision-making: The data recorded on bin cards provides valuable insights that can be used to make informed inventory management decisions, such as adjusting reorder points or identifying slow-moving items.
- Efficient Stocktaking: Bin cards facilitate the stocktaking process by providing a detailed record of stock balances, making it easier to reconcile physical stock with recorded balances.
Step-by-step Guide For Implementing Bin Card
Implementing a bin card system requires careful planning and execution. Here is a step-by-step guide to help you successfully implement a bin card system:
1. Assess Your Inventory Needs
Start by assessing your inventory management needs and determining which items and locations require bin cards. Consider factors such as the value, turnover rate, and criticality of items in your inventory.
2. Design Your Bin Card Template
Create a bin card template that suits your specific requirements. Include fields for item details, receipt information, issue information, balance calculation, and any other relevant information you need to track.
3. Train Your Staff
Train your staff on how to properly update and maintain bin cards. Emphasize the importance of accurate and timely record-keeping to ensure the effectiveness of the system.
4. Introduce a Standard Operating Procedure (SOP)
Develop a standard operating procedure for using bin cards. Clearly outline the steps for updating the card, including how to record receipts, issues, and balance calculations. Make sure everyone follows the SOP consistently.
5. Implement Regular Stocktaking
Conduct regular stocktaking to verify the accuracy of the bin card balances. Compare the physical stock levels with the recorded balances and investigate any discrepancies. Adjust the balances accordingly to maintain accurate inventory records.
6. Monitor and Analyze Bin Card Data
Regularly monitor and analyze the data recorded on the bin cards. Look for trends, identify any issues or irregularities, and use the information to make informed inventory management decisions. Adjust reorder points, identify slow-moving or obsolete items, and streamline your inventory management processes based on the insights gained from the bin cards.
7. Continuously Improve Your Bin Card System
Seek feedback from your staff and stakeholders to continuously improve your bin card system. Address any challenges or issues that arise and implement necessary changes to enhance the effectiveness and efficiency of your inventory management processes.
8. Leverage Technology
Consider leveraging inventory management software or systems that integrate with bin cards to automate data entry and provide real-time visibility into stock levels. This can streamline the bin card process and enhance overall inventory management efficiency.
Free BIN Card Template!
The bin card is a valuable tool for businesses to track the inventory levels of specific items in specific locations. It provides a detailed and comprehensive record of stock movements, enabling efficient inventory management and preventing stockouts or overstocking.
Enhance your inventory management with our free BIN card template, available in Excel format!
Ideal for businesses and warehouses, this template helps you track stock levels, movements, and inventory details with ease.
Stay organized and optimize your inventory management with this essential tool!
BIN Card Template Excel – Download
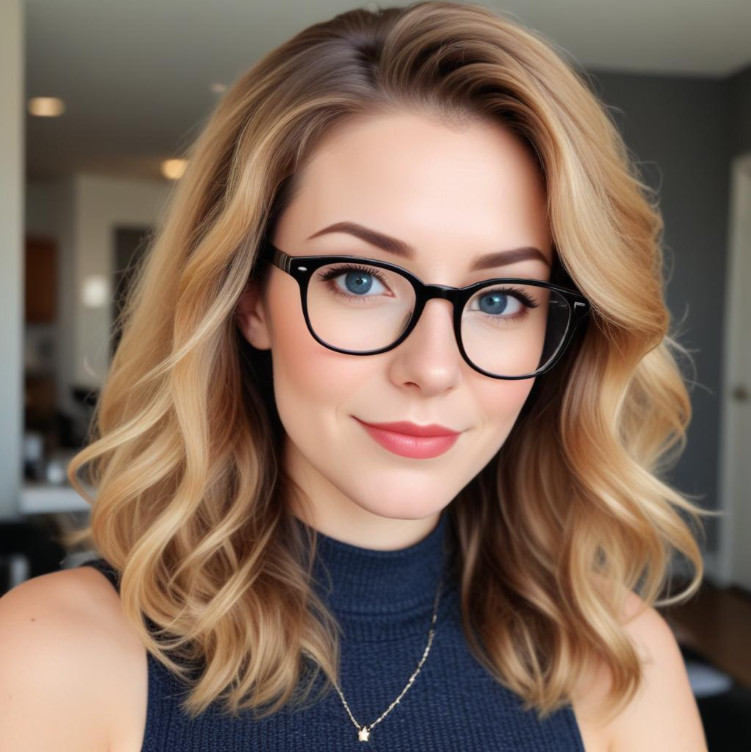
I am Huguette Prudence, the writer and curator of this website. With a profound passion for writing and reading, I strive to create insightful and engaging content. My background includes managing a small online shop and overseeing a business website, experiences that have honed my skills and broadened my understanding of effective online communication. Thank you for visiting Huguetemplate.net, where I aim to share knowledge and inspiration through carefully crafted content.